[拼音]:yali rongqi
[外文]:pressure vessel
内部或外部承受气体或液体压力、并对安全性有较高要求的密封容器。压力容器早期主要应用于化学工业,压力多在10兆帕以下。合成氨和高压聚乙烯等高压生产工艺出现后,要求压力容器承受的压力提高到 100兆帕以上。随着化工和石油化学工业的发展,压力容器的工作温度范围也越来越宽。新工作介质的不断出现,还要求压力容器能耐介质腐蚀。许多工艺装置规模越来越大,压力容器的容量也随之不断增大。在工厂内制造的压力容器单台重量就达千吨,在现场制造的球形压力容器、预应力混凝土压力容器的直径可达数十米。20世纪60年代开始,核电站的发展对反应堆压力容器提出了更高的安全和技术要求,进一步促进了压力容器的发展。许多生产工艺过程需要在压力下进行,许多气体和液化气需要在压力下贮存,因此压力容器越来越广泛地应用于各工业部门。许多新技术的发展对压力容器不断提出了新的更高的要求。如:煤转化工业的发展需要单台重量达数千吨的高温压力容器;快中子增殖反应堆的应用需要解决高温耐液态钠腐蚀的压力容器;海洋工程的发展需要能在水下几百至几千米工作的外压容器。
压力容器在使用中如果发生爆炸,会造成灾难性事故。历史上曾多次发生过使成百人伤亡的压力容器爆炸事故,甚至小型液化石油气瓶的爆炸也会造成人身伤亡。核电站用反应堆压力容器如发生事故,就会使放射性物质外逸,造成更为严重的后果。因此,防止压力容器发生事故,始终是压力容器设计、制造和使用者首要的任务。为了使压力容器在确保安全的前提下达到设计先进、结构合理、便于制造、使用可靠和造价经济等目的,各国都根据本国具体情况制定了有关压力容器的标准、规范和技术条件,对压力容器的设计、制造、检验和使用等各个方面提出具体和必须遵守的规定。随着压力容器技术的发展,在不断积累经验的基础上,标准、规范、技术条件的内容也不断得到完善和提高。
结构
压力容器主要为圆柱形,少数为球形或其他形状。圆柱形压力容器通常由筒体、封头、接管、法兰等零件和部件组成。图1中的压水堆核电站反应堆压力容器是一种典型的圆柱形压力容器。它的筒体一般是用单层钢板卷成圆柱形后焊制而成。压力容器工作压力越高,筒体的壁就应越厚。对于直径较小的厚壁压力容器,往往采用整体锻造的厚壁筒体。直径大的压力容器壁厚可达100~400毫米。压力容器有多种结构形式,如多层式、绕板式、型槽绕带式、热套式、厚板卷焊式和锻焊式等。
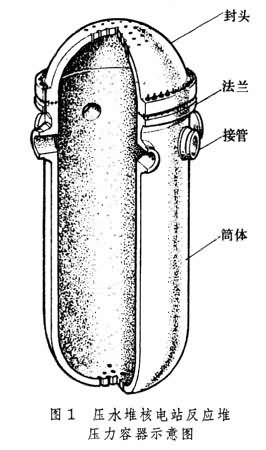
在20世纪30年代就已开始在工业上使用。这种结构的压力容器由若干个多层筒节组焊而成。各筒节由内筒和在外面包扎的层板组成。内筒厚度一般为12~25毫米,外层层板的厚度一般为 6~12毫米。图2为多层式压力容器主要制造工序和结构示意图。在内筒制成后,将层板同心地包扎在内筒外面,有钢丝绳将层板捆紧于内筒上,然后焊接层板的纵焊缝,并借包扎力和纵焊缝的焊接收缩力使层板与内筒互相贴紧,并使内筒产生一预加的压缩应力。第一层层板包扎、焊接后,用相同的方法包扎、焊接以后各层层板,达到所需要的筒体厚度为止。这种结构的优点是制造设备较简单,材料的选用有较大的灵活性,可按介质的腐蚀性选用合适的内筒材料,而层板选用一般压力容器用钢。这种结构即使在某一层钢板中出现裂缝,裂缝也只能在该层层板中扩展,不会扩展到其他层板上。在每个筒节的层板上开有通气孔,可用来监测内筒是否泄漏,以防止发生事故。安全性高是这种容器的突出优点。它的缺点是生产工序多、劳动生产率低。(见彩图)
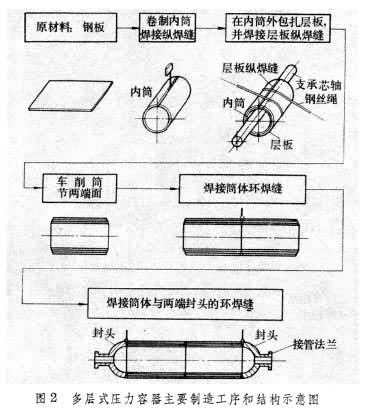
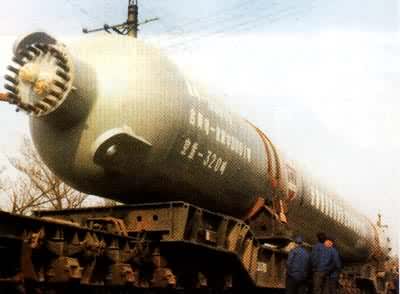
这种容器是将成卷的薄钢板连续地缠绕在内筒外面,达到所需要壁厚为止,因而不必逐层包扎层板和焊接每层层板的纵焊缝。
型槽绕带式压力容器图3为这种容器的主要制造工序。在绕带机床上对型槽钢带通电加热到红热状态,再用压辊将钢带压合到内筒表面上预先加工出的螺旋沟槽内,使之相互啮合。每绕完一层钢带后再绕下一层,直到所需的筒体厚度为止。这种结构的特点是:型槽钢带层层啮合,可使钢带层承受容器的一部分轴向力;筒体上没有贯穿整个壁厚的环焊缝;使用安全性高。这种结构的缺点是需要使用特殊轧制的型槽钢带和专用机床。
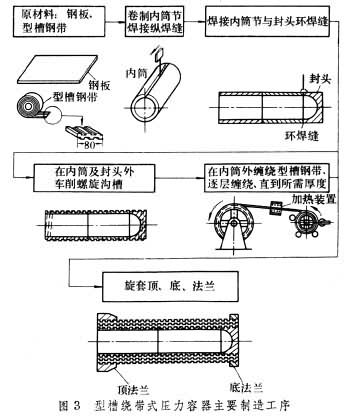
采用特殊的缠绕方法将不带沟槽的扁平钢带逐层绕于内筒上,使筒体上的扁平钢带层也能承受轴向力。内筒的厚度比型槽绕带式压力容器的内筒薄,而且无需用大型机床加工内筒外表面的沟槽。扁平钢带式压力容器是中国首创的一种高压容器,在中国的小化肥工业中已得到较广泛的应用。
热套式压力容器内筒外面套合上一至数层外筒,组成筒节(图4)。通常先将外层筒体加热使其直径增大,以便套在内层筒体上。冷却后的外层筒体就能紧贴在内筒上,同时对内筒产生一定的预加压缩应力。内筒和外筒的厚度一般相同,常用25~50毫米的钢板卷焊而成。热套压力容器用的钢板比多层压力容器的层板厚,层数少(一般2~3层,最多为5层),所以生产效率比多层压力容器高。
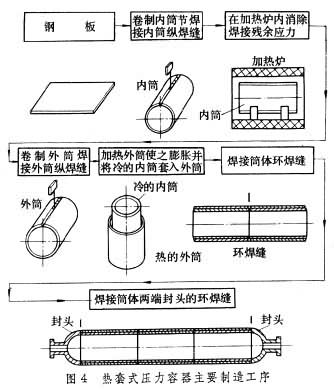
工业上有些工艺过程要在工作压力高于 100兆帕条件下进行,如高压法生产聚乙烯和人造水晶等。这时,因所使用的压力容器的壁厚很大,当容器的直径比(外径与内径的比值)增大到1.5以上时,容器筒壁上沿厚度分布的应力就很不均匀,内壁所受的切向应力和径向应力会大大高于外壁,当容器尚未达到工作压力时,内壁就过早屈服。为此,常采用预应力的措施,使容器内壁产生较大的预压缩应力,以改善容器受压时筒壁上受力状况。在结构上可采用热套式容器,控制热套过盈量以达到所要求的内壁预压缩应力;也可采用绕丝结构,在内筒的外层缠绕若干层控制预拉伸应力的高强度钢丝,以使内壁得到所需要的预压缩应力。
厚板卷焊式压力容器直接采用厚钢板卷焊成筒节,再将筒节焊制成筒体。由于受钢板生产等条件的限制,钢板厚度一般不超过200毫米。
锻焊式压力容器由锻造的筒节经组焊而成,结构上只有环焊缝而无纵焊缝。70年代以来,由于冶炼、锻造和焊接等技术的进步,已可供应570吨重的大型优质钢锭,并能锻造最大外径为10米、最大长度为4.5米的筒体锻件,因而大型锻焊式压力容器得到了发展,成为轻水反应堆压力容器、石油工业加氢反应器和煤转化反应器的主要结构形式。
当压力容器内部的内件需要取出或更换时,压力容器需要有可拆卸的端盖,因此在端盖与筒体联接处就需要采用密封结构。密封对保证压力容器正常运转极为重要。密封结构由联接件、紧固件和密封元件组成。图5是常用的几种高压容器密封结构。为使密封元件与筒体、端盖接触的密封面上达到一定的比压力,随着操作压力的增大,同一密封元件所需密封比压力也要增大。密封按施加密封力的原理分为两类。
(1)强制式密封:完全依靠紧固件通过联接件对密封元件施加密封压力,以达到密封目的。这种密封是在容器未升压前即对密封元件施加很大的预紧力,其联接件与紧固件的尺寸较大。
(2)自紧式密封:主要依靠容器内介质的压力压紧密封元件,以达到密封目的。自紧式密封所需要的预紧力小,随着容器的操作压力增高,密封比压力也不断增大,表现出优良的密封性能。在10兆帕以下工作的压力容器一般采用强制式密封,在更高压力下工作的压力容器大多采用自紧式或半自紧式密封。
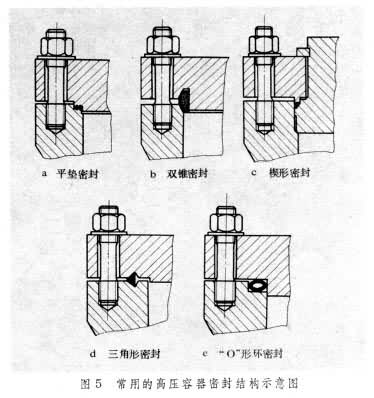
设计
压力容器的设计通常包括:分析压力容器的使用要求和操作条件,确定合理的结构形式;选择合适的材料,规定制造工艺和质量要求;按容器可能发生的失效破坏形式,确定最佳结构尺寸,使容器各部位均能满足所需的强度、刚度或不致引起断裂等要求。
在各国制定的规范中,大多数仍将容器壁简化成为均匀受力的薄膜进行处理,以薄膜应力来描述整个容器的应力水平。就圆柱形容器来说,若内部承受的压力为p,平均直径为d,筒壁厚度为δ,则沿切向的薄膜应力。规范要求的应力
t应小于规定的许用应力。然而,容器各部位的实际应力状态是很复杂的,如容器开孔边缘的最大应力可达薄膜应力的2倍以上,但在设计容器时,因采用了较大的安全系数,整个容器的应力水平仍在安全范围之内。为了避免容器发生脆性破坏,设计中除对材料要求具有足够的强度(屈服点和抗拉强度)外,还要考虑冲击值等要求。
在实际使用中,压力容器的破坏大多是由于腐蚀、疲劳、辐照和容器器壁中存在过大的缺陷等原因造成的。因此,按常规的强度设计有时还不够严密,还应区别不同情况进行特殊设计。如对高温压力容器必须按持久强度进行计算,因为在这种情况下温度对材料的性能有重大的影响。对于操作压力或温度频繁变动的压力容器,压力或温度的反复升降还可能引起疲劳失效,对这类压力容器应当进行疲劳强度设计。在存在缺陷的情况下,还应根据疲劳裂纹扩展理论对容器的使用寿命作出估算。对安全性要求极高的核电站的反应堆压力容器,必须用有限元法和其他方法对容器各部位的应力进行较为精确的计算,并从许用应力、极限承载能力、安全条件和疲劳寿命等方面加以限制。此外,在设计中还须考虑介质引起的腐蚀、中子辐照引起的材料脆化、地震和失水事故等引起的动载荷等危及容器安全的因素。为了防止反应堆压力容器因存在过大的缺陷而破坏,在核压力容器规范中已开始采用断裂力学判据,按容器中允许的缺陷采用安全系数来控制许用应力,目的在于笼统地估计许多难以确定的因素。若把各种与设计有关的参数按随机变量作统计处理,寻求其分布规律,便可定量地求出压力容器在运行中的失效概率,即可对压力容器进行可靠性设计。
选材
很多压力容器造成事故的重要原因之一是选用材料不当。例如,采用焊接性差的钢材焊制压力容器,容易在焊接接头中产生裂缝,一些危险的裂缝会在使用中导致事故。有些镍铬不锈钢的压力容器,常因钢号或成分选用不当,在使用中发生晶间腐蚀、应力腐蚀等形式的破坏。选用铁素体钢制造低温压力容器时,如钢的转变温度高于容器的工作温度,则容器工作时容易发生脆性破坏。选材应满足压力容器操作条件要求,具有良好的加工工艺性,符合有关设计和材料标准的规定,并且经济上合理。大多数压力容器由钢制成,也有的压力容器选用铝、钛等有色金属和玻璃钢、预应力混凝土等非金属材料制造。
用于制造压力容器的金属材料经过制造时的焊接和热处理等工艺后,往往因金相组织变化等原因降低材料的性能。例如,有些牌号的镍铬不锈钢经焊接后抗晶间腐蚀性能显著恶化;某些合金钢经焊接后焊缝或热影响区的韧性会显著降低。因此,选材时必须考虑材料经过制造加工后性能仍能满足操作条件的要求。钢中的微量杂质元素(例如,氢、氧、硫、磷、铜、锑、锡和砷等)会降低压力容器用钢的可焊性、韧性、抗辐照脆化性和耐蚀性。因此,在选择压力容器用钢时不仅选择钢号,有时还选择冶炼方法,提出对钢中某些杂质元素的限制。
选材不仅要考虑机械强度的要求,也需要考虑其耐蚀性。介质的成分、温度和压力等操作条件,往往对材料的耐蚀性有很大的影响。为了正确选用材料,必须了解准确的操作条件和材料在此条件下发生腐蚀破坏的形式。
质量检验
为保证压力容器的安全使用,在制造时必须按照有关标准、规范对压力容器的原材料和加工制造过程进行严格的质量检验。压力容器在运行中,小的缺陷因腐蚀或疲劳等原因有可能扩展成为大缺陷,或出现新的缺陷。因此,对投入运行的压力容器也需要进行定期检验。压力容器的检验内容主要有:对材料的化学成分和力学性能的常规理化检验;对焊接接头的各种性能检验;对压力容器各部分存在的各类缺陷的无损检测;用高于操作压力的液体对容器进行耐压试验。
质量检验在压力容器制造过程中占重要的地位。在有些反应堆压力容器的生产周期中一半时间用于质量检验。