作为纺织印染大国,我国每年排放印染废水高达30亿m3,占全国工业废水排放量的35%。印染废水中含有多种类别的染料、浆料和助剂,其成分复杂、色度高、难于生物降解,且随着印染工序的不同污染物组分差异很大,属典型的难降解有机废水。
常规的处理方法主要包括:ABR+生物接触氧化、混凝+MBR、水解酸化+生物接触氧化等组合工艺[1,2]。鉴于该类废水产生量大、处理难度高的特点,研究高效稳定的处理与回用工艺有着重要的价值。本文提出水解酸化+固定化生物滤池+混凝反应为主体的废水处理工艺,出水通过连续微滤膜(CMF)+RO系统再生后,根据企业不同用水需求,进行分质回用。通过将该工艺应用于实际工程设计,不仅对企业废水污染减排和水资源高效利用有着重要的影响,也期望能为同类企业的废水处理技术研发和应用提供科学资料和借鉴。
1 废水处理系统
1.1 背景概况
某企业从事针织印染生产,采用的主要染料为活性染料和部分分散染料,其废水日排放量达3 450m3/d,废水中以有机污染物为主要成分,另外还包括油脂、盐类以及生产时附加的表面活性剂、助剂、酸碱等。取该厂区总排口的污水进行水质分析,如表1所示。

由表1可见,该厂印染废水水质波动较大,pH较高,色度变化大,BOD5/COD为0.21~0.34,平均值为0.26,废水可生化性较差。
1.2 废水水量及设计水质
考虑可能产生的不可预见废水量,设计日处理量为3 600m3/d的污水处理系统,设计进出水水质如表2所示。污水经集中处理后作为企业的中水水源全部再生回用,根据企业生产用水的性质和功能要求,其水质要分别达到企业内部规定的软化水水质标准和生产新水水质标准;经过膜系统分离后产生的浓盐水应处理后达到《纺织染整工业水污染物排放标准》(GB 4287-2012)企业直接排放要求。

1.3 工艺流程、主要构筑物及设备
1.3.1 工艺流程
采用水解酸化+固定化生物滤池为主体的废水处理工艺,出水通过CMF+RO双膜系统进行分质回用,工艺流程见图1。

1.3.2 主要构筑物及设备
(1)格栅/中和池。在中和池前设置机械格栅,废水经细格栅进入集水井,去除原水中漂浮物、石子等颗粒物质,防止提升泵堵塞。细格栅采用回转式格栅除污机,单机宽度1 500mm,栅条间距1mm。中和池为钢筋混凝土结构,半地下式结构,数量1座,尺寸20m×15m×5m,HRT=10min,设置安全护栏和检修扶梯、潜流泵3台(2用1备)。
(2)调节池。废水经中和后流入调节池,数量1座,钢筋混凝土结构,半地下式结构,尺寸20m×15m×5m,HRT=10h,设置安全护栏和检修扶梯、潜流泵3台(2用1备),并设计穿孔管曝气,进行预曝气。
(3)气浮池、水解酸化池。气浮池是在水解酸化池前置气浮单元,尺寸8m×2.4m×2m,水力停留时间:20min,通过气浮作用分离水中的悬浮物。水解酸化池HRT=8h,总有效池容1 200m3,尺寸为24m×10m×5m,钢筋混凝土结构(防腐),数量1座。
(4)固定化曝气生物滤池。采用曝气生物滤池填料上固定高效硝化细菌的形式,该池具有很强的硝化作用,在硝化除氨氮的同时还能去除一定量的COD,HRT=12h。有效容积1 800m3,尺寸为20m×20m×5m,钢筋混凝土结构(防腐)结构,数量1座,固定床高效滤料:900m3,设置充氧风机(1用1备)。
(5)混凝沉淀池。固定化曝气生物滤池的出水投加药剂后进入反应池,水流紊动使微絮粒相互接触碰撞形成较大絮体后,在沉淀池中去除。反应池采用折板式,加设扰流单元达到所需的水力条件。单池工艺尺寸8m×5m×1m,设计流量为120m3/h,设计流速为0.11~0.3m/s,HRT=20min;沉淀池采用平流式,单池工艺尺寸20m×10m×3m(分4格),设计流量120m3/h,水平流速7mm/s沉淀时间4h。
(6)CMF/RO双膜系统。双膜系统设计处理规模:3 600m3/d,包括连续微滤膜(CMF)和反渗透(RO)两大部分。CMF系统有4台单机,设计为3用1备。RO系统2台单机,设计为1用1备,日产水量2 400m3。CMF作为反渗透进水的前处理,主要去除废水中微粒及有机物等,可使进水SDI<3,达到RO进水要求和工业补充新水的要求。RO主要用于脱除废水中的可溶性盐、胶体、有机物及微生物,出水水质达到一级RO脱盐水要求。
(7)Fenton氧化-气浮池。Fenton氧化池1座,氧化后与气浮连用,通过气浮的泥水分离作用将Fenton氧化池浮渣除去,该池设计流量为100m3/h,共HRT=2h,总有效池容100m3,钢筋混凝土结构(防腐),尺寸为2m×2m×2.5m,池内壁做玻璃钢防腐,池内设搅拌装置,加药装置3套,分别为酸、硫酸亚铁、过氧化氢加药装置。
(8)污泥浓缩池。污泥储池有效容积为40m3,尺寸为3m×3m×5m,用以储存从预处理系统的浮渣及生化系统定期排放的剩余活性污泥。沉淀排出上清液,浓缩污泥经污泥调理罐调理为易脱水的污泥,经隔膜压滤机脱水为泥饼,外运至有关资质单位进行后续处理处置。
(9)其他。设备间内设置3台罗茨风机,2台风机供生化系统曝气(1用1备),1台供调节池预曝气并通过空气搅拌调节水质;混凝气浮2座,加药系统3套;控制室内设有电源柜1套、电控柜1套。污泥处理间设污泥调理罐1套,加药系统1套,隔膜板框压滤机1套,就地电控1套。
2 系统调试与运行
2.1 系统启动与调试
2.1.1 生化系统
由于该类废水进水B/C较低,直接进行污泥培养较困难,因此采用接种法进行污泥培养,接种污泥选用附近污水处理厂脱水后的泥饼作为菌种,含水率为85%。水解酸化池污泥投加浓度为12g/L,固定化生物滤池投加污泥浓度为8g/L。同时开启鼓风机鼓风曝气与污泥回流系统,先闷曝3d后,不断调整进水时间并逐渐增加进水量,28d后增加进水量至2 000m3/d,此时取样观察,活性污泥数量的增多,污泥沉降比约40%,污泥浓度约700mg/L,显微镜下已有一定数量的累枝虫和钟虫,说明污泥的活性与絮凝性仍然较差。维持上述工况继续运行20d后,泥水界面清晰,上清液较清澈,污泥沉降比约为30%,此时污泥驯化基本完成。之后再运行20d,并逐渐增加进水量至3 600m3/d,运行稳定后取泥水混合物样品观察,镜检发现存在大量的菌胶团、累枝虫、钟虫及极少量线虫。通过污泥性状、生物相及出水水质判断处理系统运行良好,系统接种驯化完成并进入运行阶段。
2.1.2 双膜系统
双膜系统投运时,初始产水量控制在设计水量的30%~60%。运行24h后,再增至设计产水量,以利于膜通量的长期稳定。在此系统中,连续微滤膜相当于反渗透系统的前期处理,其效果直接决定了整个膜系统运行的效果与使用寿命。反渗透系统在试运行期间电导率和压差的变化分别如图2、图3所示。

系统调试期,RO产水电导率较稳定,平均值在68.7μS/cm左右,压差平均值在0.245MPa左右。随着运行时间的增加,膜组件的压差变大,电导率去除率开始不稳定,并趋于下降,这是由于系统在运行过程中,有机物和胶体硅的吸附、无机盐的结垢以及微生物的滋生共同引起的膜元件污染现象,膜污染使水分子透过膜时所需的压力与能耗增高,因此应定期对反渗透膜元件进行清洗,RO系统在调试初期总体运行正常。
2.2 系统运行效果分析
2.2.1 预处理单元
为防止管道和水泵堵塞,废水先经过格栅去除大块杂物后,进入pH调整池调节其pH;之后流入调节池,并在调节池底部设置曝气穿孔管采用空气搅拌进行调节,减少因印染废水排放时段的变化对后续处理所带来的影响;经调节后的废水,并通过气浮装置进一步去除细小悬浮物,以减轻后续处理单元负荷。经该单元组合预处理后,如表3所示,出水平均COD为645mg/L,平均BOD5为178mg/L,平均NH3-N为28mg/L,色度约为190倍,平均SS为177mg/L,pH在8左右。

2.2.2 水解酸化、固定化生物滤池、混凝沉淀单元
如表4所示,废水进入水解酸化池后,利用水解酸化菌改善废水中改善难降解有机物的可生化性,为后续好氧处理工艺创造条件[5,6]。在水解酸化处理单元中,COD平均去除率为19.3%,BOD5为29.3%,NH3-N为14.1%,色度为39.4%,SS为20.5%。色度的大幅去除说明水解酸化过程使染料分子结构发生改变(开环、断键、裂解、基团取代和还原等),从而使染料废水的组分也相应地发生了变化。

废水经水解酸化处理后进入固定化生物滤池,该处理单元中COD平均去除率为70.3%,BOD5平均去除率为86.7%,由于通过固定化技术,将高效硝化菌固定在载体上,硝化作用效果明显,NH3-N平均去除率达40%以上。色度及SS也有较好的去除效果,去除率分别为13.6%和45.3%。之后,通过投加药剂,混凝沉淀池的水各项水质指标进一步降低。
2.2.3 双膜系统
CMF-RO系统运行效果见表5。混凝沉淀池出水进入CMF和RO系统后,各类水质指标都有较好的去除效果,生产新水由CMF产水和RO脱盐水混合调配而成,可满足不同用水需求。特别是膜对于SS的截留作用,使SS去除率达到99.6%。

2.2.4 浓盐水
反渗透过程中产生的浓盐水中仍残留一定量的生物难降解有机物,采用Fenton法对其进行深度处理。Fenton法反应过程中产生大量絮体,因此在后续增加气浮单元,其处理效果见表6。
表6 运行期CMF-RO系统进出水质
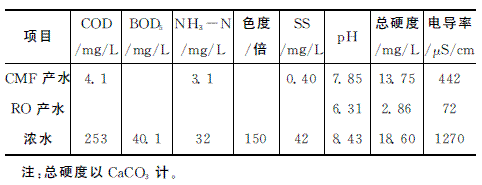
3 主要技术经济指标
根据运行数据,整个工艺运行电费包括废水处理段、再生回用和浓盐水处置三部分,其中废水处理段运行电费:0.62元/m3;再生回用段(CMF+RO系统)运行电费:2.62元/m3(CMF:0.32元/m3,RO系统2.32元/m3)。气浮池与混凝沉淀池药剂主要为PAC,投加费用为0.18元/m3。Fenton试剂为30%双氧水和硫酸亚铁,双氧水投加费用为1元/m3,其他试剂费(碱、酸、硫酸亚铁)及污泥处理费约为0.3元/m3。人工费约0.08元/m3,其他费用(如:维修费、设备折旧费、行政管理费)为0.07元/m3。最终计算出单位废水处理费为0.8元/m3;单位浓盐水处理费为1.32元/m3,单位脱盐水处理费为3.41元/m3。
4 结论
(1)采用水解酸化固定化生物滤池双膜的组合工艺处理印染废用并回用,污染物去除效果好,抗冲击负荷强,工业新水水质可根据需要由CMF产水与RO脱盐水混合调配,且其水质与脱盐水水质均满足企业用水要求;RO系统产生的浓盐水经Fenton+气浮深度处理后,出水水质达到《纺织染整工业水污染物排放标准》(GB 4287-2012)现有企业直接排放标准。
(2)该组合工艺处理费用较低,单位水量处理费0.8元/m3,单位浓盐水处理费1.32元/m3,单位再生水处理费3.41元/m3。