[拼音]:mofenli
[外文]:membrane separation
利用流体中各组分对膜的渗透率 (物质在单位推动力梯度作用下,在单位时间内经过单位膜面积的透过量)的差别实现组分分离,是一种属于传质分离过程的单元操作。膜可以是固态或液态,所处理的流体可以是液体或气体,过程的推动力可以是压力差、浓度差或电位差。
沿革
1748年法国学者A.诺勒开创了膜渗透现象的研究。20世纪40年代中期出现人工离子交换膜,开始了电渗析的工业应用。1960年,S.洛布和S.索里拉金首先用醋酸纤维素制成非对称性反渗透膜,开拓了反渗透的实际应用。1968年,美籍华裔学者黎念之最先研究乳化液膜的形成方法和渗透机理,开拓了液膜分离技术。中国自1958年开始研究电渗析,1966年开始研究反渗透,现已对膜分离技术的各个领域开展了研究工作,并推广于工业应用。
膜的类别和结构
膜分离的效能,取决于膜本身的属性。膜可分液膜和固体膜。固体膜又可分:
(1)无机多孔膜,由无机质的多孔材料构成。将胶体和不溶性微粒强制沉积于无机多孔膜上便制成动力形成膜。
(2)合成膜,通常采用醋酸纤维素、芳香族聚酰胺、聚砜、聚乙烯、聚丙烯等高分子材料制成。合成膜又分为离子交换膜、均质膜和多孔膜。离子交换膜由带有可电离的阳离子或阴离子的高分子材料所构成;均质膜是均匀的高分子薄膜;多孔膜是在铸膜液中加发孔剂,经过蒸发和凝胶分离而成的。多孔膜又分为非对称膜和复合膜。非对称膜(见图)
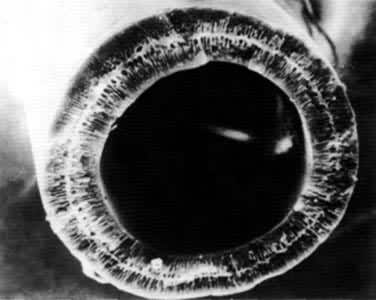
的膜体可分为表皮层和支撑层,表皮层质地致密,厚度很小(0.1~0.2μm),但它决定了膜的选择性和渗透性能;支撑层具有多孔结构,它提供必要的机械强度。膜的结构可通过调节铸膜液组成和凝胶形成条件予以控制。复合膜是以多孔膜作支撑层,覆以极薄的表皮层。用于工业分离的合成膜,可制成片状、管状和中空纤维状(见彩图)等,因此膜分离设备也随之具有多种结构形式。膜的结构形态,通常借助于电子显微镜技术、电子透射或扫描来观察。
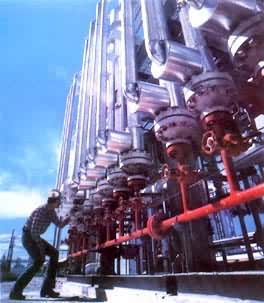
过程分类
按所用的膜,分为液膜分离和合成膜分离。液膜分离过程分为乳化液膜和固定液膜的分离过程。合成膜的分离过程(见图)包括微过滤、超过滤、反渗透、气体渗透分离、渗透蒸发、渗析及电渗析等过程。
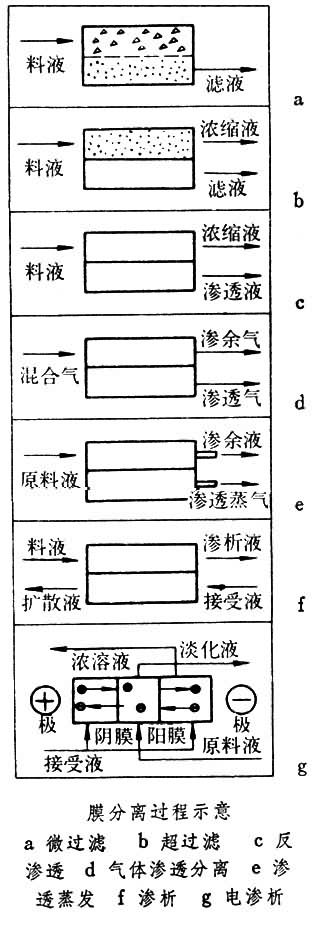
膜分离过程可简化为渗透过程。渗透过程的机理研究尚处于发展之中,有多种描述方法,目前尚未得出统一的理论。渗透的基本问题是膜内传递的概念。物质在膜内的传质通量可概括为:传质通量=渗透系数×传递推动力式中传质通量为单位时间内单位膜面积的物质透过量;渗透系数为单位时间内单位膜面积在单位推动力作用下的物质透过量;传递推动力有多种,各有其计量单位。渗透系数不仅取决于渗透物质的属性,也取决于膜材料的化学属性和膜的物理构型(见表)。
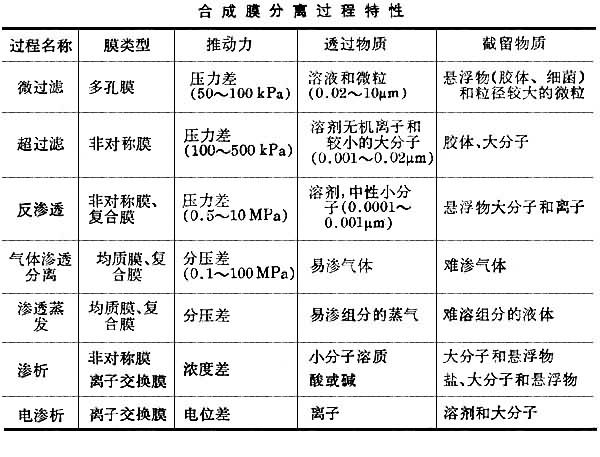
描述膜渗透机理的主要模型有:
(1)溶解-扩散模型适用于液体膜、均质膜或非对称膜表皮层内的物质传递。在推动力作用下,渗透物质先溶解进入膜的上游侧,然后扩散至膜的下游侧,扩散是控制步骤。例如气体的渗透分离过程中,推动力是膜两侧渗透物质的分压差。当溶解服从亨利定律(见相平衡关联)时,组分的渗透率是组分在膜中的扩散系数和溶解度系数的乘积。混合气体的分离依赖于各组分在膜中渗透率的差异。
溶解-扩散模型用于渗透蒸发(又称汽渗,上游侧为溶液,下游侧抽真空或用惰性气体携带,使透过物质汽化而分离)时,还须包括膜的汽液界面上各组分的热力学平衡关系。
(2)优先吸附-毛细管流动模型 由于膜表面对渗透物的优先吸附作用,在膜的上游侧表面形成一层该物质富集的吸附液体层。然后,在压力作用下通过膜的毛细管,连续进入产品溶液中。此模型能描述多孔膜的反渗透过程。
(3)从不可逆热力学导出的模型 膜分离过程通常不只依赖于单一的推动力,而且还有伴生效应(如浓差极化)。不可逆热力学唯象理论统一关联了压力差、浓度差、电位差对传质通量的关系,采用线性唯象方程描述这种具有伴生效应的过程,并以配偶唯象系数描述伴生效应的影响。
在一些膜分离过程中,会出现浓差极化现象,须在设计和操作中采取合理措施,以减少其不利影响。
应用
与传统分离技术相比,膜分离技术的优点在于过程简单,在常温下操作,能耗低,特别适宜于热敏物质的分离、浓缩和提纯。合成膜分离广泛应用于溶液脱盐、纯水和超纯水的制备,废水处理,生物制品的提纯以及气体的组分分离等。随着合成膜性能的提高和新过程的开发,膜分离技术的应用将更加广泛。液膜分离尚处于创始阶段,今后将为化工分离提供又一种有效方法。
- 参考书目
- 王振堃等著:《电渗析和反渗透》,上海科学技术出版社,上海,1980。
- P.Meares,Membranes Separation Processes,Elsevier Scientific Pub.Co.,Amsterdam,1976.